Huono vedenkestävyys, epätasainen pinta, korkea jauhepitoisuus ja epätasainen pituus?Yleisiä ongelmia ja parannustoimenpiteitä vesirehutuotannossa
Päivittäisessä vesirehutuotannossamme olemme kohdanneet ongelmia eri näkökulmista.Tässä on joitain esimerkkejä, joista voidaan keskustella kaikkien kanssa seuraavasti:
1, Kaava
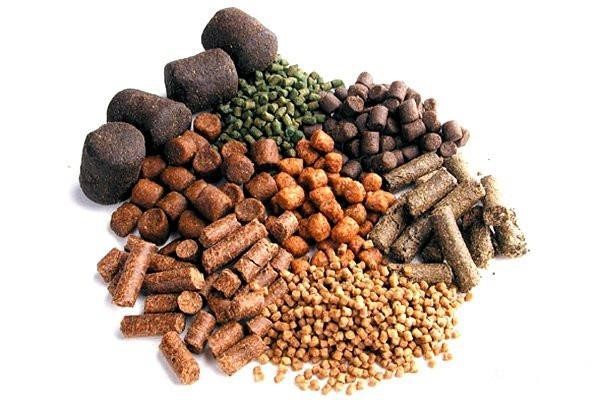
1. Kalanrehun kaavarakenteessa on enemmän raakakuituun kuuluvia jauhoraaka-aineita, kuten rypsijauho, puuvillajauho jne.Joillakin öljytehtailla on edistynyttä tekniikkaa, ja öljy paistetaan periaatteessa kuivaksi hyvin vähäisellä pitoisuudella.Lisäksi tämän tyyppiset raaka-aineet eivät imeydy helposti tuotannossa, mikä vaikuttaa suuresti rakeistamiseen.Lisäksi puuvillajauho on vaikea murskata, mikä vaikuttaa tehokkuuteen.
2. Ratkaisu: Rypsikakun käyttöä on lisätty ja kaavaan on lisätty laadukkaita paikallisia raaka-aineita, kuten riisilesettä.Lisäksi on lisätty vehnää, jonka osuus kaavasta on noin 5-8 %.Sopeutuksen kautta rakeistusvaikutus on vuonna 2009 suhteellisen ihanteellinen, ja myös tonnisato on kasvanut.2,5 mm:n hiukkaset ovat 8-9 tonnia, mikä on lähes 2 tonnia enemmän kuin aikaisemmat.Myös hiukkasten ulkonäkö on parantunut merkittävästi.
Lisäksi puuvillansiemenjauhon murskauksen tehokkuuden parantamiseksi sekoitimme puuvillansiemenjauhon ja rypsijauhon ennen murskaamista suhteessa 2:1.Parannuksen jälkeen murskausnopeus oli periaatteessa sama kuin rypsijauhon murskausnopeus.
2, Epätasainen hiukkasten pinta
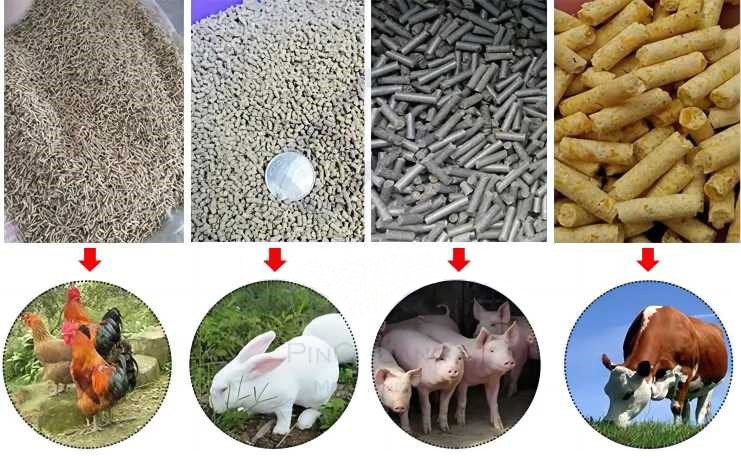
1. Sillä on suuri vaikutus valmiin tuotteen ulkonäköön, ja veteen lisättynä se on taipuvainen romahtamaan ja sen käyttöaste on alhainen.Tärkein syy on:
(1) Raaka-aineet murskataan liian karkeaksi, ja karkaisuprosessin aikana ne eivät ole täysin kypsyneet ja pehmenneet, eikä niitä voida yhdistää hyvin muihin raaka-aineisiin kulkiessaan muotin reikien läpi.
(2) Kalanrehuseoksessa, jossa on korkea raakakuitupitoisuus, koska raaka-aineessa on höyrykuplia karkaisuprosessin aikana, nämä kuplat repeytyvät muotin sisällä ja ulkopuolella olevan paine-eron vuoksi hiukkasten puristuksen aikana, jolloin hiukkasten pinta on epätasainen.
2. Käsittelytoimenpiteet:
(1) Ohjaa murskausprosessia kunnolla
Tällä hetkellä yrityksemme käyttää kalanrehua valmistaessaan bulkkiraaka-aineena 1,2 mm:n seulamikrojauhetta.Valvomme seulan käyttötiheyttä ja vasaran kulumisastetta murskauksen hienouden varmistamiseksi.
(2) Säädä höyryn painetta
Kaavan mukaan säädä höyryn painetta kohtuullisesti tuotannon aikana, yleensä noin 0,2.Koska kalanrehussa on paljon karkeakuituisia raaka-aineita, vaaditaan korkealaatuista höyryä ja kohtuullista temperointiaikaa.
3, Hiukkasten huono vedenkestävyys
1. Tämäntyyppinen ongelma on yleisin päivittäisessä tuotannossamme, ja se liittyy yleensä seuraaviin tekijöihin:
(1) Lyhyt karkaisuaika ja alhainen karkaisulämpötila johtavat epätasaiseen tai riittämättömään karkaisuun, alhaiseen kypsyysasteeseen ja riittämättömään kosteuteen.
(2) Riittämätön liimamateriaali, kuten tärkkelys.
(3) Rengasmuotin puristussuhde on liian alhainen.
(4) Öljypitoisuus ja raakakuituraaka-aineiden osuus kaavassa on liian korkea.
(5) Murskaushiukkaskokotekijä.
2. Käsittelytoimenpiteet:
(1) Paranna höyryn laatua, säädä säätimen terän kulmaa, pidennä karkaisuaikaa ja lisää sopivasti raaka-aineiden kosteuspitoisuutta.
(2) Säädä kaavaa, lisää tärkkelyksen raaka-aineita asianmukaisesti ja vähennä rasvan ja raakakuitujen osuutta.
(3) Lisää tarvittaessa liimaa.(Natriumpohjainen bentoniittiliete)
(4) Paranna puristussuhdettarengas kuolla
(5) Hallitse murskauksen hienoutta hyvin
4, Liiallinen jauhepitoisuus hiukkasissa
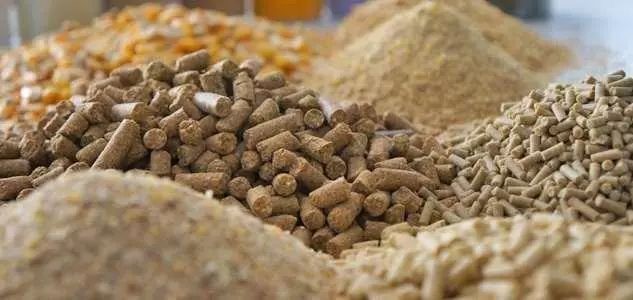
1. On vaikea varmistaa yleisen pellettirehun ilmestymistä jäähdytyksen jälkeen ja ennen seulontaa.Asiakkaat ovat ilmoittaneet, että pelleteissä on enemmän hienoa tuhkaa ja jauhetta.Yllä olevan analyysin perusteella uskon, että tähän on useita syitä:
A. Hiukkasten pinta ei ole sileä, viilto ei ole siisti ja hiukkaset ovat löysät ja alttiita jauheen muodostukselle;
B. Epätäydellinen seulonta luokittelun avulla, tukkeutunut seulaverkko, kumipallojen voimakas kuluminen, yhteensopimaton seulaverkon aukko jne.;
C. Valmiiden tuotteiden varastossa on paljon hienojakoista tuhkaa, eikä raivaus ole perusteellinen;
D. Pölynpoistossa pakkaamisen ja punnituksen aikana on piileviä vaaroja;
Käsittelytoimenpiteet:
A. Optimoi kaavan rakenne, valitse rengassuulake järkevästi ja hallitse puristussuhdetta hyvin.
B. Rakeistusprosessin aikana säädä temperointiaikaa, syöttömäärää ja rakeistuslämpötilaa, jotta raaka-aineet kypsyvät ja pehmenevät kokonaan.
C. Varmista, että hiukkasten poikkileikkaus on siisti ja käytä pehmeää teräsnauhasta valmistettua leikkausveistä.
D. Säädä ja ylläpidä luokitusnäyttöä ja käytä kohtuullista näyttökokoonpanoa.
E. Toissijaisen seulontatekniikan käyttö valmiin tuotteen varastossa voi merkittävästi vähentää jauheen pitoisuussuhdetta.
F. On välttämätöntä puhdistaa valmiin tuotteen varasto ja piiri oikea-aikaisesti.Lisäksi pakkausta ja pölynpoistolaitetta on parannettava.Pölynpoistoon on parasta käyttää alipainetta, mikä on ihanteellista.Erityisesti pakkausprosessin aikana pakkaustyöntekijän tulee säännöllisesti koputtaa ja puhdistaa pöly pakkausvaa'an puskurisuppilosta..
5, Hiukkasten pituus vaihtelee
1. Päivittäisessä tuotannossa kohtaamme usein hallintavaikeuksia, etenkin yli 420 malleissa. Syyt tähän on karkeasti tiivistetty seuraavasti:
(1) Rakeistuksen syöttömäärä on epätasainen, ja karkaisuvaikutus vaihtelee suuresti.
(2) Epäjohdonmukainen rako muottitelojen välillä tai rengasmuotin ja puristustelojen voimakas kuluminen.
(3) Rengasmuotin aksiaalisuunnassa purkausnopeus molemmissa päissä on pienempi kuin keskellä.
(4) Rengasmuotin paineenalennusreikä on liian suuri ja avautumisnopeus on liian korkea.
(5) Leikkuuterän asento ja kulma ovat kohtuuttomia.
(6) Rakeistuslämpötila.
(7) Rengasleikkuuterän tyypillä ja tehollisella korkeudella (terän leveys, leveys) on vaikutusta.
(8) Samaan aikaan raaka-aineiden jakautuminen puristuskammion sisällä on epätasaista.
2. Rehun ja pellettien laatua analysoidaan yleensä niiden sisäisten ja ulkoisten ominaisuuksien perusteella.Tuotantojärjestelmänä olemme enemmän alttiina rehupellettien ulkoiseen laatuun liittyville asioille.Tuotannon näkökulmasta vesirehupellettien laatuun vaikuttavat tekijät voidaan tiivistää karkeasti seuraavasti:
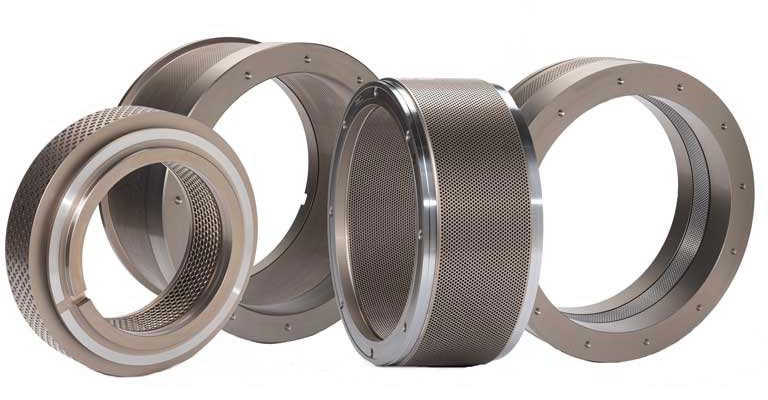
(1) Rehujen suunnittelulla ja järjestämisellä on suora vaikutus vedessä käytettävien rehupellettien laatuun, ja niiden osuus on noin 40 prosenttia kokonaismäärästä.
(2) murskauksen voimakkuus ja hiukkaskoon tasaisuus;
(3) Rengasmuotin halkaisija, puristussuhde ja lineaarinen nopeus vaikuttavat hiukkasten pituuteen ja halkaisijaan;
(4) Rengasmuotin puristussuhde, lineaarinen nopeus, sammutus- ja karkaisuvaikutus sekä leikkuuterän vaikutus hiukkasten pituuteen;
(5) Raaka-aineiden kosteus, karkaisuvaikutus, jäähdytys ja kuivaus vaikuttavat valmiiden tuotteiden kosteuspitoisuuteen ja ulkonäköön;
(6) Itse laitteisto, prosessitekijät sekä sammutus- ja karkaisuvaikutukset vaikuttavat hiukkasjauhepitoisuuteen;
3. Käsittelytoimenpiteet:
(1) Säädä kangaskaavin pituutta, leveyttä ja kulmaa ja vaihda kulunut kaavin.
(2) Kiinnitä huomiota leikkuuterän asennon säätämiseen oikea-aikaisesti tuotannon alussa ja loppupuolella pienen syöttömäärän vuoksi.
(3) Varmista tuotantoprosessin aikana vakaa syöttönopeus ja höyryn syöttö.Jos höyryn paine on alhainen eikä lämpötila voi nousta, se tulee säätää tai pysäyttää ajoissa.
(4) Säädä rakoa kohtuudellarullan kuori.Seuraa uutta muottia uusilla teloilla ja korjaa nopeasti kulumisesta johtuva painerullan ja rengasmuotin epätasainen pinta.
(5) Korjaa rengasmuotin ohjausreikä ja puhdista tukkeutunut muotin reikä välittömästi.
(6) Rengasmuottia tilattaessa alkuperäisen rengasmuotin aksiaalisuunnan molemmissa päissä olevien kolmen reikärivin puristussuhde voi olla 1-2 mm pienempi kuin keskellä.
(7) Käytä pehmeää leikkausveistä, jonka paksuus on säädetty välille 0,5-1 mm, varmistaaksesi mahdollisimman terävän reunan siten, että se on rengasmuotin ja puristustelan välisellä liitäntälinjalla.
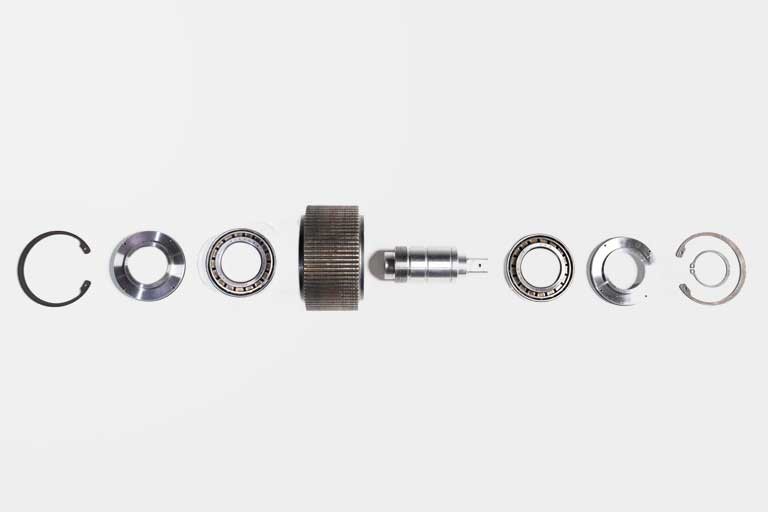
(8) Varmista rengasmuotin samankeskisyys, tarkista säännöllisesti granulaattorin karan välys ja säädä sitä tarvittaessa.
6, Yhteenveto valvontapisteistä:
1. Jauhaminen: Jauhamisen hienous on säädettävä eritelmien vaatimusten mukaisesti
2. Sekoitus: Raaka-aineiden sekoituksen tasaisuutta on valvottava sopivan sekoitusmäärän, sekoitusajan, kosteuspitoisuuden ja lämpötilan varmistamiseksi.
3. Kypsytys: Puhdistuskoneen painetta, lämpötilaa ja kosteutta on valvottava
Partikkelimateriaalin koko ja muoto: puristusmuottien ja leikkuuterien on valittava sopivat tiedot.
5. Valmiin rehun vesipitoisuus: Kuivumis- ja jäähdytysaika sekä lämpötila on varmistettava.
6. Öljyn ruiskutus: Öljyn tarkkaa määrää, suuttimien määrää ja öljyn laatua on tarpeen valvoa.
7. Seulonta: Valitse seulan koko materiaalin eritelmien mukaan.
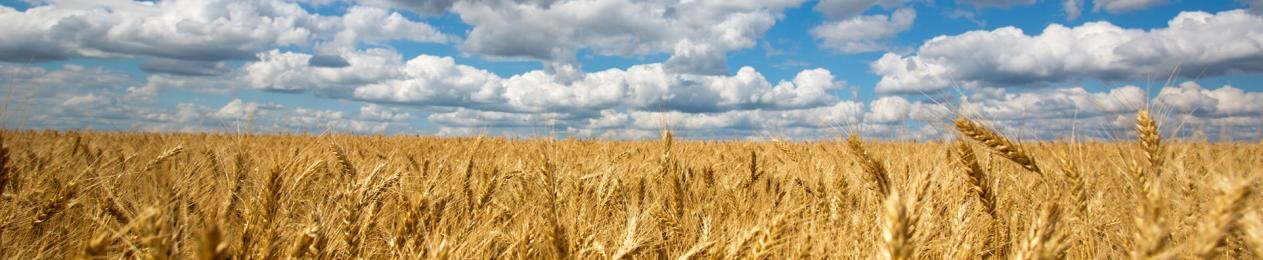
Postitusaika: 30.11.2023